Successful Deployment of Aircraft Emergency Evacuation Chutes
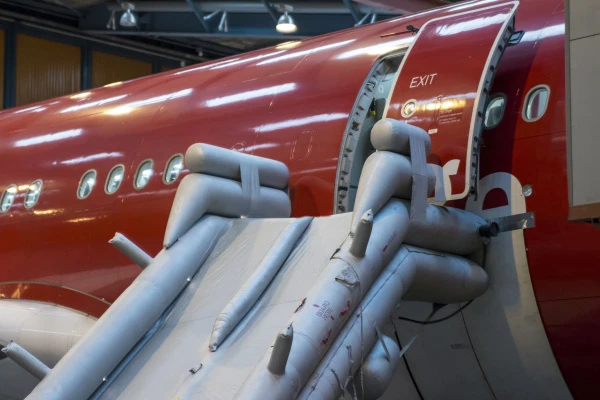
Deployed aircraft emergency evacuation chute
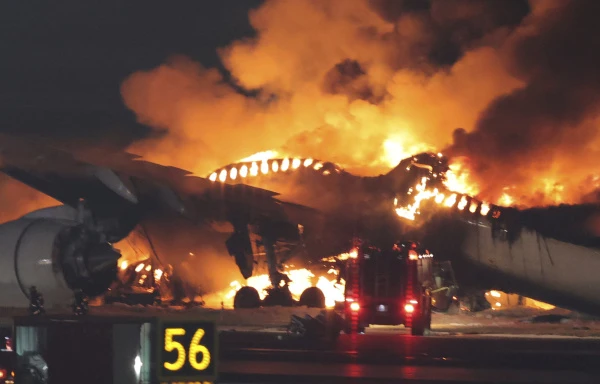
Japan Airlines runway crash & emergency evacuation on 2/6/24 via AP
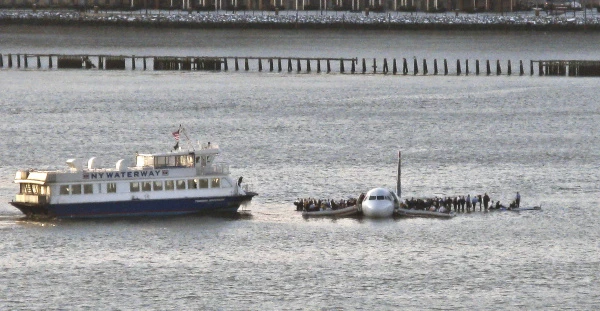
Miracle on the Hudson, 1/15/09, via AP
Unique Challenges for Machine Elements
There are many applications where Belleville springs can be stacked in arrangements to provide increased load and/or deflection, and used as a machine element — or the mechanical components of a machine. This type of application presents unique challenges that differ from bolting applications. Some of these include:
1. Cyclical loading- Belleville, like any high stressed components, can be subject to fatigue failure in high-cycle applications.
2. Tolerance on loading or displacement- Every component in a machine assembly has dimensional tolerances. This invariably leads to performance variation. The key is to understand acceptable limits of this variation and design springs to meet these requirements.
3. Space constraints- Bellevilles are often used when high loads are needed, and space is limited. It is critical to understand the envelope for any given design.
4. Friction- There is friction at all loading interfaces of a Belleville spring. This is especially true when springs are stacked in parallel. However, for each spring stacked in series, the contact is rolling, and friction is reduced. Tall stacks of springs also tend to buckle, which can add to the friction.
5. Design optimization- For any design problem, there are often multiple solutions. For example, an application requires a linear displacement of .060" at 1000 lbs. and must fit into a 1.00-inch diameter cavity. We may be able to stack three springs that have 400 lb. flat loads in parallel to meet the loading and five sets in series to meet the deflection requirement. However, another possibility would be to stack six springs that have a 1200 lbf flat load in series. The latter is a much more efficient design because fewer parts and less space will be needed and so the cost per assembly will be reduced assuming other factors such as manufacturing steps are equal. An added benefit will be reduced friction and overall weight.
6. Environment- elevated temperatures, cryogenic applications, and corrosive environments play a significant role in each design.
Aircraft Safety System Inflation Equipment
One application that considered all of these factors is for a pressure regulator that is integral for aircraft safety systems. The inflation equipment, manufactured by NMG Aerospace, is used to manage a steady flow of gas to ensure swift, proper inflation of aircraft evacuation slides in an emergency. A proprietary design comprised of a stack of Solon's Belleville springs are critical components in the regulators that regulate the flow and pressure of the ambient air that is forced to inflate the chutes. When a chute is activated by flight crew in an emergency, a small explosive blast of air travels through a hose and into the regulator before forcing the air into a chamber called the aspirator, which as several small orifices that create a venturi effect (low-pressure system). The resultant behavior aspirates (sucks in) air into the evacuation chutes causing instant inflation. When activated, the regulators have a piston that compresses the Bellevilles thus regulating the pressure.Japan Airlines Runway Collision & Evacuation
The manufacturing and inspection processes are tightly controlled, and the design must adhere to stringent testing criteria, such as precision load and friction requirements. A recent example of the application at work was showcased on January 2, 2024, when an Airbus A350 Japan Airlines aircraft collided with a Japanese Coast Guard plane shortly after touching down on the runway. Unfortunately, five of the Coast Guard members were killed, and the pilot seriously injured. However, 379 passengers and crew members on flight JAL516 survived, evacuating swiftly and safely sliding down the emergency evacuation chutes containing NMG Aerospace inflation equipment. Details from this incident have confirmed that the flight crew was able to evacuate all passengers from the burning plane in just under 18 minutes, using three escape chutes out of the plane's eight available exit doors.'Miracle on the Hudson' Landing & Evacuation
Another famous example of the successful deployment of emergency evacuation equipment on an aircraft containing Solon Belleville Springs in the regulator equipment occurred on January 15, 2009, when US Airways Flight 1549 struck a flock of birds shortly after takeoff from LaGuardia Airport, losing all engine power. With no time to turn back toward LaGuardia, or attempt a landing at a nearby New Jersey runway, pilots Chelsey "Sully" Sullenberger and first officer Jeffrey Skiles, made the calculated decision to glide the plane to ditching on the Hudson River off Midtown Manhattan. Once the order was given to evacuate, the crew began evacuating all 155 passengers through the four wing-window exits where the emergency evacuation slides were deployed. As frigid water began entering the aircraft through holes in the fuselage and cargo doors, evacuees moved to stand on the wings of the aircraft or waited on the partially submerged slides to be rescued by the NY Waterway ferries, the U.S. Coast Guard, and other numerous boats that were in the water that day. Miraculously, everyone survived with only a few serious injuries.Solon Solution: Stacking Arrangements
In addition to installing Solon Belleville Springs & Washers to the fastening system for bolted connections, using them in a stacking arrangement as structural or control components for machines ensures a proven and reliable solution for applications subjected to fatigue issues, friction, high loads, displacement, and elevated or cryogenic temperatures- that are critical to the successful operation of the equipment.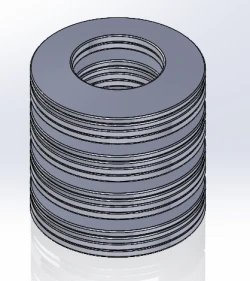
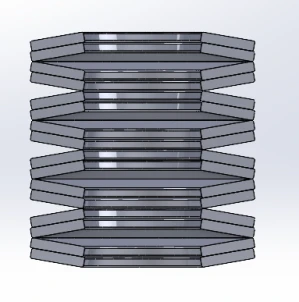
Solon Belleville Spring Washers in a stacked configuration
Solon Manufacturing Company, an industry leader on engineered solutions for critical applications, can help from design through aftermarket to ensure bolts have the correct mating parts that will effectively support design requirements. Often there are standard options already available, though a custom Belleville washer can be engineered around specifications.Additional information such as calculator tools, videos, case studies and technical white papers can be found in our resource library.
Click Here to download a PDF of this case study.